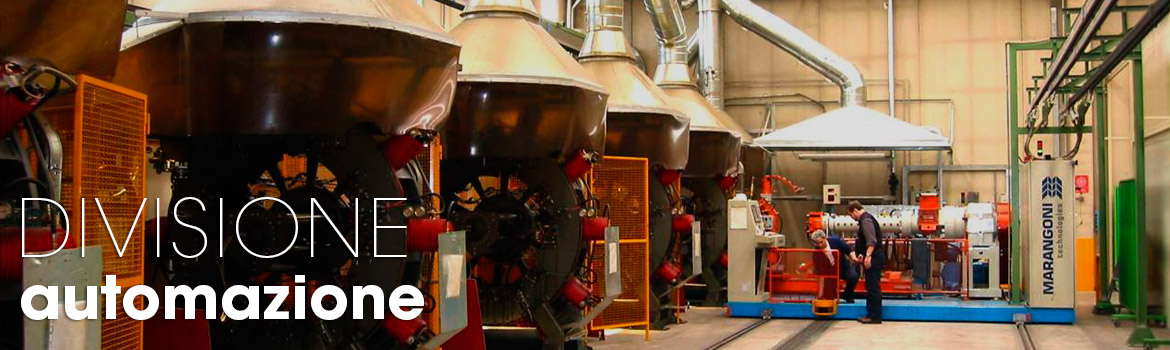
Divisione Automazione
L’attività ormai pluridecennale della Divisione Automazione del Gruppo Fantini ha portato all’acquisizione di competenze ed esperienza nei più svariati campi dell’industria di processo e di prodotto, dai classici settori della movimentazione e manipolazione di prodotti ai comparti più specifici ed impegnativi come l’industria aerospaziale.
Nel dettaglio, i settori di impiego dei prodotti Fantini sono:
- Industria aeronautica;
- Industria aerospaziale;
- Industria alimentare;
- Industria della gomma;
- Linee di trasporto e movimentazione materiali;
- Linee di imballaggio e pallettizzazione;
- Magazzini automatici;
- AGV e navette/carrelli di trasporto;
- Attrezzature di sollevamento.
La Divisione Automazione del Gruppo Fantini realizza impianti ed attrezzature tecniche con formula “chiavi in mano”, studiati di volta in volta per rispondere alle diverse esigenze di produzione e di lay-out del Cliente.
Di seguito, le fasi che scandiscono i nostri progetti:
- Sopralluoghi c/o il Cliente per recepire le esigenze/li>
- Studio di soluzioni preliminari
- Elaborazione di preventivi
- Progettazione meccanica
- Calcoli e verifiche strutturali
- Progettazione impianto elettrico e software
- Documentazione tecnica di accompagnamento del prodotto ai sensi delle Direttive Europee applicabili
- Implementazione sistemi di supervisione
- Costruzione e pre-assemblaggio meccanico ed elettrico presso il nostro stabilimento
- Collaudo interno
- Installazione e collaudo finale presso il Cliente
- Assistenza post-vendita
- Fornitura di ricambistica
Case History: Progetti nel settore AEROSPAZIO
-
Impianto di movimentazione e stoccaggio attrezzature
Per la Fiat Avio di Colleferro è stato progettato e realizzato un impianto per la movimentazione delle protezioni termiche “fuori opera” utilizzando apposite attrezzature, stampi e pallet di appoggio. L’impianto è concepito per collegare i vari locali dello stabilimento dove si svolgono le operazioni e lavorazioni sui manufatti; in particolare:
Ambiente C: in questo locale avvengono tutte le lavorazioni di stratificazione a freddo della gomma negli stampi e nei segmenti.
Ambiente di applicazione adesivi, pulizia e magazzino: questi ambienti sono ubicati fra i due ambienti principali C e D; negli ambienti di applicazione adesivi arrivano i manufatti dopo la vulcanizzazione e da questi, dopo l’applicazione dell’adesivo, vengono avviati verso la camera pulita.
Nella stazione di pulizia vengono inviate le attrezzature e gli stampi prima di essere inviati alla camera pulita.
Nel magazzino (ambiente E) vengono stoccate le attrezzature e gli stampi.
Ambiente D: in questo ambiente avvengono le lavorazioni di vulcanizzazione in autoclave della gomma, di separazione del manufatto dallo stampo e delle attrezzature di vulcanizzazione dai segmenti dopo aver terminato il ciclo in autoclave.Alcuni dei trasportatori sono configurati su due piani di scorrimento, il primo a circa 500 mm dal pavimento ed il secondo a circa 1250 mm dal pavimento stesso; nell’attraversare i locali il pavimento passa dal livello 0 m al livello 6m per ritornare al livello 0 m, per cui le quote assolute dei piani di scorrimento saranno 0.5 m, 1,25 m, 6,5 m e 7,25 m.
Opportuni elevatori/discensori consentiranno di effettuare il cambio di quota. -
Pressa di giunzione bandelle protezione termica
Per la Fiat Avio di Colleferro è stata realizzata una pressa per giunzione di nastri in gomma EPDM per alimentare la macchina di avvolgimento delle protezioni termiche dei segmenti del motore P80. La giunzione avviene mediante riscaldamento e compressione a temperatura e pressione controllate.
Il macchinario è costituito dai seguenti elementi:
Gruppo rotante guida banda in ingresso ed uscita: si tratta di due dischi rotanti posti rispettivamente all’ingresso e all’uscita della pressa; ciascun disco è completo di quattro rulli folli di guida bandelle, un rullo per ciascun formato.
Gruppo pressa: Il gruppo è costituito da due piastre fisse, una superiore ed una di base unite da quattro colonne di guida, il tutto posizionato su un bancale di supporto. All’interno delle due piastre fisse, scorrono sulle colonne di guida il piano mobile superiore ed i due piani laterali di supporto del gruppo di contenimento bandella. La pressione nella fase di giunzione bandella è applicata mediante un martinetto a vite motorizzato. Tra la testa della vite del martinetto ed il piano mobile è interposta una cella di carico per il rilevamento e controllo della forza applicata alla bandella. Sulla zona superiore della piastra mobile è posizionata la motorizzazione per la traslazione dei due gruppi di rifilatura bandelle posizionati al di sotto della piastra stessa.
Sulla piastra mobile e sulla piastra di base sono fissati, con interposizione di spessori isolanti, i due blocchi riscaldanti; i suddetti blocchi sono riscaldati mediante terne di resistenze.
Sui blocchi riscaldanti sono fissate le due matrici di larghezza adeguata alla bandella in lavorazione; le matrici sono dotate di sonde per il rilevamento e controllo della temperatura.
Al di sotto del piano mobile sono posizionati quattro distanziali registrabili per limitare la corsa del piano mobile, che fanno riscontro su altrettanti distanziali fissati sulla piastra di base.Gruppo contenimento bandelle: sui due supporti mobili inferiori, mossi verticalmente da altrettanti attuatori pneumatici, sono installati due gruppi di contenimento bandelle nella fase di sovrapposizione; ciascun gruppo è costituito da un modulo lineare pneumatico completo di lama di contenimento.
Gruppo rifilatura bandelle: posizionato lateralmente alla matrice superiore, è fissato sulla piastra mobile ed è costituito da due slitte con traslazione longitudinale a vite. Nella zona inferiore delle due slitte sono installati due moduli lineari pneumatici con traslazione trasversale. Al di sotto dei due moduli saranno installati i due supporti completi di coltelli di taglio e riscontri di posizionamento.
-
Attrezzatura di integrazione ugello e accenditore su motori Zefiro 9 e Zefiro 23
Scopo: montaggio dell’ugello e dell’accenditore sui motori ZEFIRO 9 e ZEFIRO 23
Dati caratteristici ugello/accenditore:
Ugello per Z9: diametro: 1256.4 mm; lunghezza: 1640.48 mm; massa: 225.9 Kg
Ugello per Z23: diametro: 1510.2 mm; lunghezza: 2023 mm; massa: 576.5 Kg
Accenditore per Z9: diametro: 260.75 mm; lunghezza: 601.75 mm
Accenditore per Z23: diametro: 362.4mm; lunghezza: 727mmDescrizione:
Il sistema, realizzato per l’Avio SpA – stab.to di Colleferro, è costituito da una struttura in carpenteria metallica destinata a movimentare i componenti denominati Ugello e Accenditore per il loro montaggio sui motori ZEFIRO 9 e ZEFIRO 23.La struttura è dotata di movimento lungo l’asse del motore e di movimento verticale per consentire il centraggio dei componenti rispetto al motore; inoltre è previsto un movimento di rotazione per consentire il ribaltamento dell’ugello dalla posizione di ricezione dal carroponte alla posizione di montaggio sul motore. Tutti i movimenti sono manuali e comandati da appositi volantini.
Dal momento che il motore è realizzato in fibra di carbonio, è fondamentale controllare la forza di spinta durante l’introduzione dei componenti sul motore; per tale scopo sono state installate opportune celle di carico dotate di visualizzatore attraverso il quale l’operatore tiene sotto controllo il valore di forza e arresta il movimento di inserimento al raggiungimento del valore massimo consentito.
Al termine dell’inserimento di un componente, tutta la struttura viene sollevata per mezzo di un carroponte e portata in corrispondenza dell’altro lato del motore per l’inserimento dell’altro componente. Inoltre dal momento che i motori Z9 e Z23 hanno dimensioni diverse la struttura è montata su delle guide a terra che consentono di posizionare la macchina seconda in funzione del motore.
-
Attrezzature per movimentazione segmenti vettore spaziale Ariane 5
CARRELLI A SERVIZIO AUTOCLAVE
Si tratta di attrezzature adibite al supporto dei segmenti durante il trattamento di vulcanizzazione in autoclave; per questo motivo si tratta di sistemi privi di motorizzazione propria e con a bordo solo elementi in grado di resistere alle condizioni operative del ciclo (T=190 °C, atmosfera di azoto a P=1,1 MPa). Il carrello non è semovente dunque deve essere introdotto ed estratto dall’autoclave mediante altri mezzi di trasporto.TRASPORTATORE LONGITUDINALE
La funzione di questi trasportatori è quella di spingere o trainare i carrelli di cui sopra all’interno dell’autoclave o fuori dall’autoclave al termine del processo di vulcanizzazione. Durante la traslazione le due attrezzature sono vincolate meccanicamente attraverso l’inserimento manuale di un perno di fissaggio; un sensore rileva la presenza del perno o meno e dà di conseguenza il consenso al movimento di traslazione dei due elementi.TRASPORTATORE TRASVERSALE
La funzione principale di questo trasportatore è quella di spostare il carrello con o senza segmento a bordo dalla postazione di carico alle vie di corsa che conducono all’autoclave e da queste alla postazione di scarico segmento dopo la sua vulcanizzazione. Questa attrezzatura è costituita essenzialmente da un telaio di supporto in acciaio dotato di ruote motorizzate per la traslazione trasversale e di sistema di sollevamento per svincolare il carrello dai binari.CARRELLO MOVIMENTAZIONE SETTORI DA AMBIENTE D-ALTO A D-BASSO
Il carrello è costituito da un telaio realizzato in acciaio, sopra il quale su apposite guide di scorrimento si muovono due selle opportunamente sagomate per l’alloggiamento dei segmenti.
Ciascuna sella è dotata di propria motorizzazione per attuare lo spostamento in funzione della lunghezza del segmento. Il comando del movimento delle selle si aziona da pulsantiera fissa posta in prossimità del trasportatore.BILANCINO
Si tratta di un sistema automatico per il sollevamento dei segmenti ARIANE 5. Il bilancino viene sollevato e movimentato a mezzo di un carroponte e portato in corrispondenza delle postazioni di prelievo dove, dopo una serie di operazioni automatiche di centraggio e rotazione, aggancia il segmento.
Progetti nel settore CHIMICO
-
Costruzione ed installazione di un elevatore a C
Per la Procter & Gamble di Pomezia, è stato progettato e realizzato un elevatore a “C” con catene gripper idoneo alla movimentazione di fustini di detersivo. L’elevatore a “C” è realizzato con struttura in acciaio al carbonio e ripari in acciaio inox.
L’elevatore riceve le scatole singole o i fardelli dalla linea esistente e le trasferisce da quota +1000 mm a quota +4685 mm.
Ha la regolazione in apertura delle catene gripper regolabile tramite motoriduttore e contatore numerico per la visualizzazione della posizione raggiunta.Le catene gripper sono installate su un equipaggio mobile guidato mediante pattini a ricircolo di sfere su guide il tutto comandato da martinetti a vite motorizzati mediante motoriduttore al fine di consentire la regolazione in altezza delle catene per permettere la presa dei fustini in modo corretto mantenendo fissi il piano di trasporto del nastro inferiore di alimentazione e superiore di scarico.
Produttività 120 fustini/min. -
Tramoggia elevatrice linea 1 – Goldie
Per la Procter & Gamble di Pomezia, è stato progettato e realizzato un impianto per l’alimentazione dei flaconi vuoti nella macchina orientatrice Pace. La fornitura è composta di N° 2 tramogge elevatrici rispettivamente per la Linea#1G e per la Linea#3G.
Nello specifico una tramoggia elevatrice è composta da una tramoggia che tramite un piano di calpestio permetterà all’operatore di rovesciare i contenitori dei flaconi al suo interno; un nastro di trasporto posto sul fondo della tramoggia invia i flaconi al nastro inclinato che a sua volta tramite una tramoggetta di scarico alimenterà la macchina a valle.
La capacità della tramoggia è sufficiente per contenere N° 1000 flaconi nel formato 2.5 litri . -
Magazzino Automatico
Presso lo stabilimento Lever di Pozzilli (IS) è stato realizzato l’ampliamento del magazzino automatico aggiungendo una ulteriore corsia gestita da un nuovo traslo elevatore. Il prodotto da movimentare è il pallet formato da scatole o flaconi di detersivo.
Le caratteristiche del prodotto da movimentare sono le seguenti:- Dimensioni pallet: 1200x800x2050 mm
- Peso massimo pallet: 1000 kg
La fornitura consiste in:
- n° 6 trasportatori a catena come baie di carico e scarico pallets
- n° 1 coppia di scaffalature metalliche.
Progetti nel settore ALIMENTARE
-
Macchina per movimentazione cialde
L’impianto in oggetto è stato progettato e realizzato per le società italiana SAGIT e francese MIKÓ, per eseguire il trasferimento delle cialde sul nastro di alimentazione del forno. L’impianto è composto da:
- N° 12 nastri trasportatori con motorizzazioni indipendenti (lu=1200 mm, la=150 mm, inclinazione: 30°)
- N° 12 manipolatori dotati di carrelli pick&place con motorizzazioni indipendenti
- N° 1 nastro recupero scarti (lu=3400 mm, la=350 mm)
- Quadro elettrico e pulpito di comando.
Nella costruzione dei vari elementi sono stati utilizzati i criteri di igiene e pulizia tipici dell’industria alimentare; in particolare la progettazione e la realizzazione sono state eseguite in modo da escludere la presenza di saldature e di superfici piane su cui possa depositarsi sporcizia.
CICLO DI FUNZIONAMENTO
Le cialde vengono caricate manualmente in pile sui nastri trasportatori a facchini; durante tale fase le cialde passano tra le sponde calibratrici che ne definiscono il diametro massimo.
Sui nastri le cialde avanzano fino ad impegnare la fotocellula di presenza (fibra ottica) che corrisponde alla posizione di presa dei manipolatori.
Giunte le cialde nella posizione di presa, i bracci di presa dei manipolatori ruotano verso il basso per mezzo di una camma, mentre il carrello trasla verso il nastro di alimentazione.
Quando il carrello arriva nel punto di presa, la ventosa si porta a contatto con la superficie della cialda e ne effettua la presa; quindi, il carrello inizia la traslazione con la cialda in posizione verticale e, superato l’ingombro del nastrino, viene effettuata la rotazione del braccio mediante il sistema a camma.
Quando il carrello giunge nella posizione di deposito, la cialda viene posizionata all’interno dei riferimenti posti sul nastro di alimentazione del forno NIC e rilasciata su di esso. -
Linea produzione coni
L’impianto in oggetto è stato progettato e realizzato per effettuare la movimentazione di pallets e vassoi a servizio della linea di produzione coni, presso lo stabilimento italiano SAGIT e francese MIKÒ .
Nella costruzione dei vari elementi di impianto sono stati utilizzati i criteri di igiene e pulizia tipici dell’industria alimentare; le strutture dei trasportatori, elevatori e asse index sono realizzate in acciaio INOX AISI 304, la struttura dei manipolatori è realizzata in acciaio al carbonio verniciato, mentre il gruppo mobile del manipolatore e l’organo di presa sono realizzati in alluminio.
La pila formata dai vassoi pieni, proveniente dall’area Bakery, viene depositata sul primo trasportatore della zona di carico ed avanza fino ad impegnare l’ultima stazione di accumulo; da qui i vassoi vengono prelevati singolarmente dal manipolatore disimpilatore, traslati e depositati sul primo dei trasportatori a catena che formano la linea di trasporto vassoi pieni in quota (+2560 mm); al termine del disimpilamento il pallet rimasto vuoto viene inviato alla zona di trasporto pallets vuoti.
Dalla linea di trasporto i vassoi pieni vengono trasferiti, uno alla volta, mediante un trasferitore ortogonale ed un trasportatore a catena, nell’area di produzione fino a raggiungere la zona di scarico accoppiati (incarto+biscotto); qui il vassoio viene preso in carico e centrato allineando le file del vassoio con i canali delle corsie di scarico della linea di riempimento coni, dopodichè avviene lo scarico mediante un sistema costituito da spintori a comando pneumatico.
Completato lo scarico, i vassoi vuoti vengono inviati ad un elevatore, passando su trasportatori a catena e su un trasferitore ortogonale; l’elevatore porta i vassoi a quota +5285 mm, dove vengono scaricati su una serie di trasportatori a catena di accumulo attraverso i quali giungono ad un discensore che li riporta a quota +2560 mm scaricandoli sulla postazione di prelievo di un manipolatore impilatore che preleva il vassoio a quota 2560 mm e lo deposita a quota +560 mm su un pallet di servizio in attesa.
Al termine dell’impialmento, la pila di vassoi vuoti viene trasferita su un trasportatore a catena e da qui al trasportatore di scarico dal quale viene prelevata mediante carrello a forcole.
Progetti nel settore PNEUMATICO
Magazzino automatico carcasse
Linea di pallettizzazione fasce battistrada
Linea di finitura anelli battistrada
Impianto automatico produzione anelli battistrada
Linee di raffreddamento a servizio estrusore
Macchina avvolgitrice anelli battistrada
Impianto di pallettizzazione fasce battistrada
Linea di scarico pressa Saspol
Terminale linea calandra gomma per pneumatico
Manipolatore per la pallettizzazione coperture vulcanizzate
Manipolatore per carico e scarico carcasse su catena di trasporto
-
Magazzino automatico carcasse
Presso lo stabilimento Trelleborg Wheels Systems è stato realizzato un magazzino automatico per lo stoccaggio intermedio delle carcasse provenienti dalle Confezionatrici e dirette, dopo opportuna stagionatura, ai Vulcanizzatori BOM.
La carcassa viene depositata dall’operatore nella postazione d’ingresso e trasferita automaticamente alla postazione di prelievo di un manipolatore che provvede a sollevarla e depositarla su un vassoio vuoto.
Il vassoio con la carcassa viene successivamente inviato al magazzino automatico per lo stoccaggio; il vassoio è quindi trasportato fino al corridoio centrale dove opera il trasloelevatore che lo preleva e lo deposita in una delle 144 postazioni del magazzino per mezzo di uno shuttle.
Dopo opportuna stagionatura e chiamata dall’operatore, la carcassa (contenuta nel vassoio) viene trasferita fino alla postazione d’uscita per la riconsegna. Qui l’operatore la preleva ed il vassoio vuoto viene pulito tramite apposita spazzolatrice e automaticamente ricircolato.
-
Linea di pallettizzazione fasce battistrada
Per il gruppo Marangoni è stato progettato e realizzato un impianto per effettuare la pallettizzazione dei rotoli di fascia battistrada destinati al mercato della ricostruzione dei pneumatici.
Esso è composto da una serie di nastri e rulliere a servizio di una macchina fasciatrice e di un pallettizzatore. La fascia battistrada arrotolata viene scaricata sul trasportatore di uscita dell’avvolgitore (a quota 450 mm) e da qui trasferita sul nastro ad accumulo in salita che la conduce a quota 1000 mm.
Quando il rotolo arriva sulla rulliera con curva a 90°, l’operatore vi applica una etichetta di identificazione, quindi la fascia entra all’interno della macchina fasciatrice dove viene centrata ed avvolta con 2,4 o 6 strati di film. Al termine della fasciatura, il rotolo viene trasferito sulla rulliera posta all’interno del pallettizzatore e non appena urta una apposita battuta un sensore comanda la discesa del manipolatore che preleva la fascia, la trasla ed infine la deposita sul pallet.
Tale ciclo di lavoro viene ripetuto fino al completamento dei due pallet che possono differenziarsi per il numero di rotoli per strato e per numero di strati.
Per consentire le operazioni di carico e scarico dei pallets in condizioni di totale sicurezza, la parte frontale del pallettizzatore è protetta con una barriera optoelettronica che provvede ad arrestare qualsiasi movimento pericoloso in caso di intercettazione dei suoi raggi.
-
Linea di finitura anelli battistrada
Per il gruppo Marangoni (Marangoni Tread e Marangoni North America) sono state realizzate delle linee di finitura per gli anelli stampati sugli impianti Alpha Ring; in queste linee gli anelli vengono spazzolati, soluzionati e avvolti per la pallettizzazione.
Ciascuna linea è costituita dai seguenti elementi e postazioni:- postazione di carico manuale degli anelli sui cestelli
- trasportatori a servizio macchine di raspatura e soluzionatura, per una lunghezza complessiva di circa 40 m
- n° 2 macchine di raspatura
- n° 1 macchina di soluzionatura
- postazione di ispezione
- n° 1 avvolgitrice
- n° 1 elevatore/discensore a servizio linea di ricircolo cestelli vuoti
- linea superiore di ricircolo cestelli vuoti
- n° 1 discensore/elevatore a servizio linea inferiore
- n° 2 scale alla marinara e passerella per manutenzione linea superiore di ricircolo cestelli.
-
Impianto automatico produzione anelli battistrada
L’impianto in questione, realizzato per diversi stabilimenti della Marangoni (Marangoni Tread, Marangoni North America, Ellerbrock) è adibito alla produzione di anelli di gomma vulcanizzati a partire dall’estruso grezzo. L’impianto è costituito da:
- carrello portaestrusore
- n° 6 macchine centripete di tipo STANDARD o SPECIAL ad anima rotante complete di manipolatore per scarico automatico
- n° 1 linea a servizio centripete
- N° 1 linea automotore a servizio tagliobave
- n° 2 tagliobave autodimensionante.
Il carrello portaestrusore, traslando su guide a terra e partendo dalla prima pressa, serve in modo sequenziale le centripete apponendo sull’anima in rotazione la quantità di estruso stabilita per il formato di anello in questione. Al termine dell’apposizione l’anima rientra, gli stampi si chiudono radicalmente verso l’anima ed inizia il ciclo di vulcanizzazione che si conclude con lo scarico automatico dell’anello sul manipolatore presente sul lato sinistro della macchina e con la chiamata del carrello a servizio centripete.
Quest’ultimo, giunto in corrispondenza della macchina che ha effettuato la chiamata, si dispone con la sella di scarico in posizione bassa dando il consenso allo scarico; ricevuto l’anello, esso viene bloccato, portato in quota e condotto in corrispondenza della postazione di trasferimento sul carrello automotore a servizio tagliobave.
Al segnale di carrello pronto, il discensore viene sbloccato e fatto scendere fino alla quota di scarico, quindi l’anello viene trasferito sull’automotore mediante uno spintore pneumatico. A questo punto il carrello trasla fino a portarsi in corrispondenza del tagliobave impostato per quel formato di anello e lo deposita su di esso; quindi il tagliobave ruota nella posizione di lavoro ed avvia il ciclo di sbavatura al termine del quale l’operatore, manualmente, provvede alla rimozione delle bave trasversali ed allo scarico dell’anello.
-
Linee di raffreddamento a servizio estrusore
Per il gruppo Marangoni (Marangoni do Brasil e Marangoni Tread North America) sono state realizzate due linee di raffreddamento della gomma in uscita da un estrusore. La fornitura è costituita da un trasportatore di alimentazione estrusore e da una serie di rulliere che conducono la striscia di gomma alle vasche di raffreddamento.
Queste ultime sono disposte su quattro o cinque livelli (a seconda del layout) e sono dotate di nastri Intralox sui quali transita la fascia. All’uscita dalle vasche di raffreddamento la gomma passa su un nastro trasportatore con taglierina per il taglio a misura della striscia.
Le fasce così ottenute giungono poi ad un trasferitore che le conduce alla stazione di pesatura; le fasce sono poi avviate alla linea di ritorno dove vengono avvolte ed evacuate sulla rulliera di scarico dalla quale l’operatore le preleva con un partner.
Per consentire di eseguire agevolmente le operazioni di incorsamento iniziale della striscia e di manutenzione, è presente una passerella su tutta la lunghezza delle vasche, con accessi alle due estremità.
-
Macchina avvolgitrice anelli battistrada
La macchina, fornita al Gruppo Marangoni, è stata progettata e realizzata per effettuare l’avvolgimento automatico degli anelli battistrada provenienti da una linea di raspatura e soluzionatura.
La macchina riceve l’anello da avvolgere mediante l’azione di un apposito espulsore presente sulla linea di ricircolo cestelli in corrispondenza della avvolgitrice. L’espulsore provvede a spingere l’anello di gomma sulle forche dell’avvolgitrice che, ricevuto il prodotto, si mettono in rotazione determinando la formazione dell’involto.
Durante la fase di avvolgimento viene interposto uno strato di politene, erogato da uno svolgitore motorizzato, fra uno strato e l’altro dell’anello per evitare che le superfici a contatto aderiscano una sull’altra. Al termine dell’avvolgimento il politene viene tagliato mediante un dispositivo a filo caldo. La conformazione cilindrica dell’involto viene garantita mediante l’azione di due rulliere di contenimento semicircolari che si portano a contatto dell’involto durante l’avvolgimento dello stesso. Terminata l’avvolgitura, ’anello viene ruotato ulteriormente per consentire l’applicazione di nastro adesivo sulla sua circonferenza; il nastro adesivo viene erogato da un apposito gruppo nastratore e tagliato in automatico mediante un coltello.
L’involto così ottenuto viene fatto “cadere” per gravità su una apposita sella mediante un movimento di retrazione delle forche. A questo punto la sella, che per accogliere l’involto si era portata in quota proprio al di sotto delle forche, si abbassa e trasla orizzontalmente portandosi in corrispondenza di una rulliera alla quale si rende solidale mediante l’inserimento di un perno su un’apposita sede. Quindi con movimento di ribaltamento della sella e della rulliera avviene il deposito dell’anello su quest’ultima. Dopo il ribaltamento tale rulliera provvede al trasferimento dell’anello su una rulliera inclinata a valle.
La macchina è interamente protetta con recinzioni in rete metallica che segregano gli elementi mobili pericolosi; inoltre per facilitare le operazioni di manutenzione e regolazione in quota è presente una scala che consente agli operatori di raggiungere agevolmente i vari elementi.
-
Impianto di pallettizzazione fasce battistrada
Questo insieme di macchine, realizzate per il Gruppo Marangoni, svolge la funzione di impianto di pallettizzazione ed è posizionato a valle delle due linee di raspatura, soluzionatura, avvolgitura e fasciatura.
I rotoli di gomma proventienti dalle due linee a monte, avvolti e fasciati con film trasparente, transitano su nastri Intralox fino a raggiungere una stazione in cui vengono riposizionati in base alla posizione che dovranno assumere nel pallet. Continuando il percorso le fasce giungono prima in corrispondenza di una etichettatrice dove gli viene apposta un’etichetta e successivamente alla postazione di prelievo del manipolatore fasce. Quest’ultimo preleva alternativamente i rotoli da ciascuna delle due linee e li deposita sul relativo pallet.
Al termine di uno strato, il manipolatore preleva una interfalda dal magazzino apposito e la deposita sopra alle fasce, quindi continua la formazione del pallet. Quando entrambi i pallet sono completi, una navetta a due postazioni scorrevole su binari a terra, si porta in corrispondenza di essi ed avviene il loro trasferimento a bordo di quest’ultima. Contemporaneamente due pallet vuoti, transitando su appositi trasportatori a tre catene, raggiungono le postazioni di riempimento pallet ed un secondo manipolatore preleva (uno alla volta) dai magazzini pallet vuoti altri due pallet e li posiziona sui trasporti di alimentazione delle postazioni di riempimento pallet.
La navetta conduce i pallet su una linea di trasporto a servizio di una fasciatrice e, dopo la fasciatura, i pallet proseguono su dei trasporti a valle dai quali vengono rimossi dall’operatore con un muletto.
-
Linea di scarico pressa Saspol
Per il gruppo Marangoni sono state realizzate tre linee di scarico dalle presse Saspol. Al termine del ciclo di vulcanizzazione della pressa le fasce vengono prelevate da un manipolatore (facente parte integrante della pressa stessa) e scaricate sui nastrini della linea di scarico. La linea è composta da:
- nastri di raccolta fasce piane pressa 10.5 m: si tratta di ventuno nastri Intralox di lunghezza circa 2500 mm e larghezza 250 mm con interposti alle estremità dei piani elevabili per regolare l’entrata delle fasce alla linea di taglio bave e avvolgimento
- macchina di taglio bave longitudinali
- dispositivo festonatore necessario per consentire l’avvolgimento della fascia a velocità costante
- avvolgitore
- rulliere di scarico
-
Terminale linea calandra gomma per pneumatico
Per il gruppo Marangoni sono state progettate e realizzate alcune linee a valle della Calandra destinata al trattamento, avvolgitura, nastratura e scarico della foglia di gomma in uscita dalla Calandra.
All’uscita dalla calandra, la tela passa attraverso quattro tamburi di raffreddamento; tali tamburi, di diametro circa 700 mm, sono realizzati in acciaio e sono dotati di giunti rotanti per il collegamento con l’impianto dell’acqua di raffreddamento. Superati i rulli, la tela giunge su una rulliera inclinata dove viene cosparsa di polverino di gomma; l’alimentazione del polverino è garantita da un sistema di tramogge e trasportatori a coclea.
Dopo essere stata cosparsa di polverino, la tela passa attraverso la stazione di spazzolatura che ha lo scopo di distribuire uniformemente il prodotto ed eliminare le eccedenze di deposito. A valle della spazzolatura, transitando su una rulliera orizzontale in quota, la tela giunge ad un tamburo foratore; prima di essere forata, però, la tela passa attraverso una serie di tamburi di rinvio che provvedono ad accoppiarla con un film di politene proveniente da un bancale di distribuzione posizionato a terra. Poiché la tela, in questa lavorazione, deve rimanere sempre tesa, e poiché la calandra la mantiene sempre in movimento, per consentire la fermata dell’aspo avvolgitore al termine dell’avvolgimento di una bobina è presente una stazione polmone a due anse (festonatore).
A valle della stazione polmone, la gomma viene avvolta su un subbio di cartone posizionato manualmente su un aspo a tre bracci. Questa soluzione è legata alla produzione continua della calandra che obbliga l’avvolgimento su un secondo braccio quando il primo è terminato e deve essere scaricato. Per lo scarico della bobina l’operatore deposita la stessa su un dispositivo carrellato dotato di culla elevabile e ribaltatore che consente di ricevere il rotolo in posizione orizzontale (posizione di scarico dall’aspo) e di portarlo in posizione verticale.
L’ispezione e la manutenzione sui componenti posizionati in quota risulta agevole grazie alla realizzazione di una passerella con scala di accesso. -
Manipolatore per la pallettizzazione coperture vulcanizzate
Per la Marangoni Tyre di Anagni è stato progettato e realizzato un sistema di pallettizzazione coperture composto da un portale cartesiano con due ponti indipendenti. È un magazzino dinamico in grado di preordinare nelle due aree di buffer, i pneumatici provenienti dal controllo visivo per codice di prodotto. La pinza di presa è idonea al prelievo/deposito delle singole coperture e alla formazione di pile di coperture di altezza max 1500mm.
Il magazzino è suddiviso longitudinalmente in due aree. È alimentato da un sistema di trasporti che ricevono in ingresso le coperture caricate manualmente da un operatore su bilancelle nel reparto di controllo visivo e scaricate automaticamente da quest’ultime da
un meccanismo a comando elettropneumatico. I trasporti in testa alimentano, per mezzo di un trasportatore brandeggiante, una doppia linea longitudinale di trasporti che servono indipendentemente le due fila di rulliere di mezzeria delle aree di buffer del magazzino.I pneumatici, identificati grazie alla lettura del codice a barre con sistemi barcorde, giungono sulla rulliera di prelievo e vengono trasferiti nell’area di buffer per mezzo di due robot ad assi cartesiani (uno per sezione) che effettuano le traslazioni sui due assi orizzontali complanari, mentre attraverso una pinza, effettuano il prelievo verticale delle singole coperture. La pinza si posiziona al centro della cavità del pneumatico e tramite l’apertura dei bracci effettua una pressione sulla gomma sollevandola. I robot cartesiani hanno prestazioni che consentono di movimentare fino a 500 gomme/ora.
Il buffer è completamente mappato (438 posizioni a terra su tutto il magazzino, corrispondenti ad altrettante possibili pile di gomme) in maniera tale da consentire movimentazioni tracciate. Una volta completata la preparazione di una pila ad asse verticale, essa viene prelevata e trasferita presso l’area di pallettizzazione. I robot prelevano la singola pila di gomme da terra e la depositano su specifici unità di carico, pallet, costituiti da piastre metalliche inforcabili da carrelli elevatori Un’unità di carico finita, può essere composta generalmente da quattro, tre o due pile di coperture di ugual codice e misura.
Ciascun ponte è alimentato da una linea pallets indipendente con disimpilatore. I pallets sono stoccati in cataste a non più di sette livelli e trasferiti attraverso trasporti a catena al disimpilatore. Uno per volta sono inviati all’interno del magazzino; qui vengono trasferiti attraverso apposita navetta in corrispondenza dell’area di pallettizzazione. Quando il pallet è pieno, viene indirizzato verso la rispettiva uscita e prelevato da operatore con transpallet elettrico.
-
Manipolatore per carico e scarico carcasse su catena di trasporto
Per la Marangoni Tyre di Anagni,è stato progettato e realizzato un sistema per il caricamento delle carcasse sulla catena di trasporto R8. Il sistema prevede il prelievo delle carcasse da carrelli o da trasportatori aerei per le coperture provenienti dalle linee di produzione ed il deposito delle stesse sul trasporto a bilancelle R8.
Il carico avviene mediante robot antropomorfo, munito di apposito gripper, che deposita la carcassa su un meccanismo a pantografo fornito di una culla mobile. La culla posiziona il centro della cavità del pneumatico in corrispondenza della traiettoria di movimento delle bilancelle consentendone la presa. Il lotto proveniente dalle linee ha la precedenza sul lotto proveniente dal carrello.
La tipologia di carcassa in prelievo è individuata rispettivamente dalla lettura del codice a barre del carrello, al quale è associata una tipologia di copertura o mediante lettura del codice a barre posto sulla copertura per quelle proveniente dalle linee. Il PLC dell’impianto comunica al server aziendale, i record delle carcasse scaricate dai carrelli (bar-code carrello e bar-code carcasse) e di quelle provenienti dai trasportatori aerei (lettura del bar-code sul cerchietto della carcassa).
Tutto ciò è completato da un sistema di movimentazione automatico carrelli composto da un sistema di alimentazione carrelli pieni costituito da una corsia con capacità di tre carrelli pieni e sistema di avanzamento motorizzato e forchette di aggancio agenti sul tubolare di base del carrello per trascinamento; navetta di trasferimento carrello dalla corsia carrelli pieni alla postazione di svuotamento e relativa corsia uscita carrelli vuoti di costruzione analoga alla corsia alimentazione carrelli pieni.
L’apertura dei ripiani del carrello è gestita da un dispositivo automatico. E’, inoltre, presente una rulliera folle di accumulo scarti delle carcasse non riconosciute e un trasporto di raccordo dalle linee di produzione alla postazione di prelievo composto da nastri Intralox. Il sistema è in grado di movimentare complessivamente 500 carcasse/ora.
Case History: Progetti nel settore LINEE DI IMBALLAGGIO E PALLETTIZZAZIONE
-
Linee automatiche di confezionamento scatole di monete euro
Presso l’Istituto Poligrafico e Zecca dello Stato sono state installate due linee automatiche per il confezionamento di rotolini di monete Euro in scatole e per la pallettizzazione delle scatole stesse.
Ciascuna linea è costituita da due tratti: linea di confezionamento e linea di imballaggio. La funzione dell’impianto è quella di formare scatole contenenti rotolini di monete (linea di confezionamento) ed inviarle alla linea di imballaggio dove vengono chiuse con nastro adesivo, reggiate, etichettate e, infine, depositate su pallet.
L’impianto riceve i rotolini da quattro macchine confezionatrici poste lungo un nastro (ciascuna macchina riversa i rotolini su un canale del nastro) e li avvia ad una macchina inscatolatrice. Qui vengono formati tanti strati di rotolini quanti sono quelli previsti per il formato in produzione (eventualmente con interposizione di interfalde di cartone per ottenere un migliore riempimento della scatola), dopodiché avviene il trasferimento dentro una scatola di cartone precedentemente formata da una formatrice cartoni.
-
Impianto automatico di confezionamento rotoli di carta
L’impianto, realizzato per l’Istituto Poligrafico e Zecca dello Stato, è concepito per realizzare il confezionamento in scatole dei rotoli di carta utilizzati per le giocate del Gioco Lotto.
Una linea, a monte dell’impianto, effettua la formazione dei rotoli e la loro movimentazione in corrispondenza di un piano, dotato di apposite guide, sul quale i rotoli saranno trasferiti per mezzo di un apposito manipolatore; successivamente, un altro manipolatore effettua la presa di una fila di rotolini per volta (6 rotoli) ed il deposito, previo ribaltamento, su un nastro Intralox; su tale nastro è presente un lettore di barre che consente di leggere il codice dei rotolini.
Nel caso il codice corrisponda con quello aspettato il rotolo continua il suo percorso, mentre nel caso il codice non sia corretto viene emesso un segnale acustico ed il rotolo in questione non viene fatto proseguire oltre (il nastro si arresta ed un operatore deve rimuovere il rotolo e ripristinare la linea). I rotoli iungono, disposti su due file di tre rotoli ciascuna, in corrispondenza di un tunnel di termoretrazione dove vengono impacchettati con un film trasparente; successivamente il pacco arriva ad una macchina inscatolatrice dove un manipolatore a ventose effettua la presa del pacco ed il deposito all’interno di una scatola preventivamente formata.
La scatola chiusa con nastro adesivo giunge, poi, ad una tavola rotante dove viene prima etichettata e successivamente ruotata di 90° per consentire alla scatola di avanzare sul fronte del lato corto. Infine, un nastro Intralox conduce la scatola alla postazione di prelievo di un pallettizzatore; quando due scatole sono presenti nella postazione di prelievo, un dispositivo di presa a ventose effettua la presa delle scatole ed il deposito sul pallet; quest’ultimo è poggiato su appositi riscontri ad altezza variabile che consentono di effettuare il deposito sempre alla stessa quota.
Case History: Progetti nel settore LINEE DI TRASPORTO E MOVIMENTAZIONE
-
Impianto di raccolta e accumulo bobine carta Tissue
Le bobine provenienti da una macchina fasciatrice giungeranno, disposte in posizione orizzontale, su un ribaltatore dotato di opportuna sella di contenimento. Quest’ultima è dotata di uno spintore e di rulli folli inferiori per consentire un agevole accostamento della bobina al piano verticale ribaltabile; inoltre una delle due sponde della sella è incernierata in modo di consentirne l’apertura, dopo il ribaltamento, per svincolare la bobina.
A valle del ribaltatore è presente una navetta per effettuare il trasferimento della bobina in corrispondenza dei nastri di accumulo. La navetta sarà gestita in modo che essa si autocentri con il primo nastro di accumulo in funzione del diametro della bobina, trasmesso attraverso il segnale dato da una serie di fotocellule, in modo da depositare la bobina centrata rispetto al nastro.
La linea di accumulo è costituita da cinque nastri Intralox di lunghezza circa 6500 mm cadauno, capaci di accogliere due, tre o quattro bobine a seconda del diametro. Il sistema di trasferimento da un nastro all’altro è tale che quando un nastro è pieno tutte le bobine vengono trasferite sul nastro a valle. Quando le bobine giungono all’ultimo nastro della linea vengono prelevate con un apposito mezzo di sollevamento.Tutti i trasporti sono realizzati con nastri Intralox in Acetal; il piano di scorrimento è costituito da due nastri dì larghezza 800 mm con interspazio centrale di 400 mm, per una larghezza totale di 2000 mm. L’impianto si compone dei seguenti elementi (rif. ns. disegno 04-1006-00):
- n° 1 ribaltatore con sella di contenimento e trasportatore a nastro Intralox in Acetal
- una navetta con trasporto a bordo in nastro Intralox
- n° 5 trasporti a nastro Intralox ognuno lunghezza=6500 mm largh. totale=2000
- impianto elettrico e software di gestione con PLC Siemens S7
- protezioni intorno all’area di ribaltamento bobina e traslazione navetta
- protezioni antiurto in corrispondenza della zona di scarico bobina.
-
Linee di movimentazione pallet a servizio presse
L’impianto, realizzato per lo stabilimento Cobarr SpA di Anagni, è adibito alla movimentazione di pallets vuoti verso le presse ed alla evacuazione di pallet pieni in uscita dalle presse verso una linea di scarico. L’impianto si può suddividere in tre settori:
- Linea alimentazione pallet vuoti, costituita da: rulliera di carico pallets vuoti,disimpilatore pallet, rulliera di accumulo a sei posti pallet, discensore con trasportatore a catena, trasportatore a catena a servizio discensore, trasportatore a catena a servizio navetta.
- Linea di carico/scarico presse, costituita da: navetta con due piattaforme mobili (shuttle), n° 21 baie di carico/scarico presse.
- Linea evacuazione pallet pieni, costituita da: n° 1 trasportatore a catena a servizio navetta, n° 1 trasportatore a catena a servizio elevatore, n.1 elevatore con trasportatore a catena, n° 2 rulliere di accumulo a sei posti, n° 1 rulliera di scarico pallets pieni.
-
Impianto di legatura, pesatura e trasporto billette di alluminio
L’impianto in oggetto, progettato e realizzato per eseguire in automatico le operazioni di pesatura, reggiatura e trasporto di billette di alluminio, è in produzione presso l’Alcoa Italia, stabilimento di Portoscuso (CA). Esso è composto da una serie di macchine, posizionate a valle dell’impianto esistente di movimentazione e taglio billette, che eseguono le operazioni di:
- allineamento billette, trasporto billette nella postazione di formazione pacco, formazione pacco,
- trasporto pacco nella postazione di reggiatura e pesatura, compattamento billette, pesatura pacco,
- reggiatura pacco con inserimento di tacchi di legno, trasporto del pacco reggiato nella postazione di marcatura, marcatura billette,
- trasporto pacco all’esterno e formazione pila, accumulo delle pile.
Le zone pericolose dell’impianto sono protette con protezioni in rete e barriere optoelettroniche.
-
Impianto handling billette di alluminio
Per la società Alcoa Italia, stabilimento di Portovesme (CA) è stato realizzato un impianto di movimentazione billette di alluminio.
A partire dall’estrazione dal pozzo di colata, le billette vengono prima adagiate su un trasportatore, poi condotte ad una stazione di controllo; da qui, le billette danneggiate vengono dirottate su una rulliera apposita, mentre le billette idonee proseguono verso una stazione di formazione strato dalla quale un manipolatore preleva il numero di billette stabilito e le deposita su una piattaforma girevole.
Ultimata la catasta, dove fra i vari strati di billette vengono interposti dei distanziali, la piattaforma ruota di 90° per permettere alla caricatrice Bernotti di prelevare la catasta stessa e trasferirla ad uno dei forni di omogeneizzazione.
Al termine dell’omogeneizzazione e del raffreddamento, la catasta torna sulla piattaforma girevole che dopo aver ricevuto il carico ruota di 90° per consentire il disimpilamento; il manipolatore preleva dalla catasta uno strato di billette ed uno di distanziali, depositando le prime su un trasportatore e le seconde nell’apposito magazzino. Avanzando sul trasportatore le billette giungono in corrispondenza di un trasferitore che preleva una billetta per volta e la deposita su una apposita rulliera.
Da questa le billette arrivano alla stazione di carico di una navetta che ne carica un numero adeguato e le trasporta sul bancale di carico della Sega Wagner. All’altra estremità della rulliera si trovano il bancale Elhaus ed un trasferitore; il bancale può svolgere le funzioni di alimentazione del forno di omogeneizzazione Elhaus oppure può inviare le billette provenienti dall’impianto Elhaus alla navetta o, infine, può ricevere le billette scartate all’inizio del ciclo.
-
Impianto di caricamento cerchioni da gommare
Questa macchina o, più propriamente, insieme di macchine, è stata realizzata per la Caterpillar (U.S.A.), per essere integrata in un impianto più complesso. L’impianto è stato progettato e realizzato per effettuare in automatico la movimentazione di cerchioni da “gommare” verso una giostra rotante e di cerchioni “gommati” da questa verso una postazione di uscita.
I cerchioni vengono movimentati su appositi pallets dotati di appositi supporti di sostegno. L’impianto è dotato di una zona di carico/scarico costituita da tre trasportatori a catena; su questi ultimi giungono i pallets con il cerchione lavorato quindi, dopo aver rimosso il carico, su di essi viene caricato il nuovo cerchione da gommare. Al termine del carico l’operatore dal pulpito di comando esegue l’avanzamento del pallet che procede fino al trasportatore a monte della postazione di prelievo del caricatore; a questo punto l’operatore imposta sul pulpito di comando delle macchine adibite alla gommatura il codice relativo al tipo di cerchione da lavorare: tale codice verrà trasmesso al PLC affinchè le macchine si predispongano per il formato da trattare.
Quando il caricatore riceve dalla giostra (non fornita) il consenso al carico del cerchione, il pallet avanza sul trasportatore posto al di sotto del dispositivo di presa, il quale dopo essersi posizionato con la pinza orientata verso il basso, scende fino alla quota prestabilita per la presa, quindi apre i braccetti della pinza e per finire solleva il cerchione e lo ruota di 90° per presentarlo frontalmente alla giostra.
Eseguiti i movimenti sopra citati, il caricatore avanza, su binari fissati al pavimento, verso la giostra e superato l’ingombro del trasporto sottostante si porta verticalmente in asse con essa; al termine della traslazione, il caricatore invia alla giostra un segnale di cerchione in posizione e, con movimenti coordinati dei dispositivi di presa del caricatore e della giostra avviene il passaggio del cerchione su quest’ultima che ruotando lo porterà alla zona di gommatura.
A lavorazione eseguita la giostra presenta il cerchione “gommato” nella stessa posizione dalla quale era stato prelevato ed invia al caricatore un segnale di consenso al prelievo. Quest’ultimo si posiziona opportunamente e, con movimenti coordinati dei dispositivi di presa avviene il trasferimento sulla pinza del caricatore che ad operazione ultimata arretra e ruota la pinza di +90° o –90° a seconda del tipo di cerchione.
Infatti, se non è previsto il ribaltamento il cerchione verrà semplicemente rilasciato sul pallet sottostante, che ricevuto il carico avanzerà sui trasportatori a valle fino a raggiungere la zona di scarico; se, invece, è previsto il caricamento un apposito manipolatore con pinza si porterà in posizione, prenderà in carico il cerchione e lo porterà in corrispondenza di un sollevatore.
Contemporaneamente il pallet vuoto raggiungerà il piano del sollevatore, verrà portato in quota e la pinza del manipolatore rilascerà su di esso il cerchione, quindi il pallet con il cerchione a bordo verrà portato alla quota degli altri trasporti sui quali il pallet transiterà fino a raggiungere la postazione di carico.